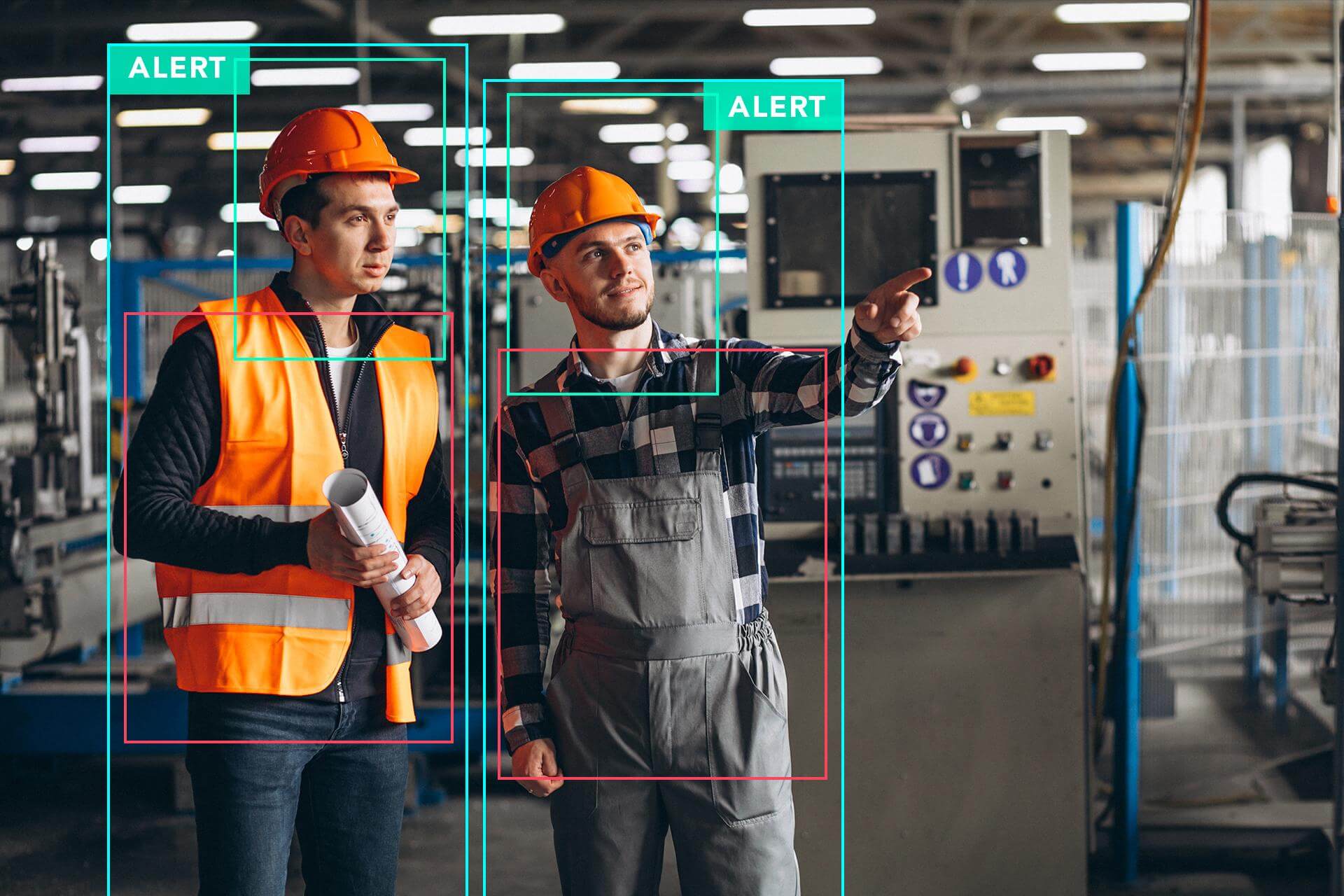
EHS 4.0: What You Need to Know About the Digital Transformation
Environmental, health and safety (EHS) management has always had three main goals: to keep people safe, minimize negative impact on the environment and keep operations running productively and without incident. This means adhering strictly to compliance regulations and looking for new ways to increase profitability while decreasing incident rates.
Why Traditional EHS Management Isn’t Enough
The goals of EHS management have stayed the same, but the means of achieving them have changed as technology advances and opens the door to new risks, challenges and opportunities.
The digital revolution—known as Industry 4.0—has completely revamped the way companies structure their business models, plan their processes and measure their performance. This brings an entire new wave of business and operational risks, but also new opportunities to optimize business models and performance.
In terms of EHS management, however, many organizations are stuck in traditional models that operate in silos and lack the data capabilities of mature processes. LNS Research reports that 46% of companies say that lack of cross functional collaboration is a top EHS performance challenge.
Adopting EHS 4.0 allows EHS organizations to make use of cyber-physical systems that connect their people, equipment, data and processes in a new way.
What is EHS 4.0?
EHS 4.0 includes the use of sensor-enabled equipment, cloud computing applications, mobile capabilities and Big Data analysis to digitally transform EHS processes. It is not the technology itself, but rather the framework—enabled by technology—that allows organizations to take their EHS initiatives to the next level.
EHS 4.0 doesn’t intend to replace traditional EHS management techniques. Instead, it utilizes digitalization of EHS with a focus on the integration of people, processes, technology and performance. EHS leaders can use this approach to pinpoint opportunities for improvement and integration of EHS into business strategy.
According to LNS Research, the seven dimensions of EHS 4.0 are:
- Strategic. EHS 4.0 is based on alignment of EHS initiatives and strategic business leadership to bring overall value to an organization through EHS management.
- Systematic. EHS management now relies on process standardization, harmonized systems and advanced analytics.
- Risk-based. Factoring risk into all processes through technology creates a proactive approach for predicting and preventing adverse events.
- Connected. EHS 4.0 promotes collaboration across departments, locations and processes, breaking down silos and integrating systems at every level of operation.
- Smart. The right tools filters and analyzes large volumes of data and presents it as useful information for data-driven decision-making.
- Agile. As surroundings change, EHS systems should fully adapt, with the scalability and capability to create and deploy new processes as needed.
- Engaged. EHS 4.0 engages the workforce through collaboration based on common objectives and an overall culture of operational excellence.
Catching up to the Digital Transformation
Recently, EHS organizations have been behind other industries when it comes to digital transformation. But investing in Industry 4.0 benefits EHS operations just as much as other industries, if not more.
Revamping asset reliability could drastically reduce equipment-caused injuries and environmental emissions. Engaging your workforce with technology turns them into “connected workers,” which are more valuable. With better situational awareness, exposure monitoring and understanding of ergonomic impact, the workforce can be more efficient while providing real-time data feedback to help higher-level processes improve.
There is an excellent opportunity for EHS business leaders to embrace the Digital Transformation and explore the possibilities of EHS 4.0.
By : EtQ LLC